

Kodak fully endorses Dwayne's processing of 35 mm films, but Dwayne's Super-8 process is not supported because it requires more agitation. Kodak no longer processes Kodachrome film and instead subcontracts the processing work to Dwayne's Photo, an independent facility in Kansas, which as of 2009, is the only remaining Kodachrome processing facility. The Parliamentary committees for Culture and Education and Internal Market and Consumer Protection studied the matter. On 25 July 2006, extensive documentation about Kodak's Lausanne Kodachrome lab's impending closure was sent to the European Parliament by the Dutch office of the European Parliament because, although located in Switzerland, the facility served all of Europe, and its closure would affect European photographers. The loss of processing availability further accelerated the fall in Kodachrome sales. Many Kodachrome processing laboratories, both Kodak-owned and independent, closed because of the decreasing volume of business. Kodak gradually discontinued Kodachrome products, and on 22 June 2009, Kodak announced Kodachrome would no longer be manufactured. The use of slide film, in general, declined in the 1980s and 1990s, which, combined with competition from Fuji's Velvia slide film, caused a drop in Kodachrome sales. The film is finally washed to remove chemicals that may cause deterioration of the dye image, dried, and cut. The film is then fixed, making these silver halides soluble and leaving only the final dye image. The metallic silver is converted back to silver halide salts following color development using a bleach solution. For example, the red-sensitive layer forms a cyan dye. A color developer then creates the fogged image, and exhaustion products form a color dye in the color that is complementary to the layer's sensitivity. Filters exist between each layer to prevent light from exposing the incorrect layer. Re-exposure exposes the silver halides not developed by the first developer, effectively fogging them. The film is developed using a developer containing phenidone and hydroquinone, which forms three superimposed negative images, one for each primary color.Īfter washing out the first developer, the film undergoes three re-exposure and re-development stages. This effectively precludes amateurs or small laboratories from processing Kodachrome.įirst, the antihalation backing is removed with an alkaline solution and washed. The process is complex and exacting, requiring technicians with extensive chemistry training and large, difficult-to-operate machinery. The current process is designated Process K-14. Kodachrome processing has undergone four significant alterations since its inception. These effects can sometimes cause a slight loss of sharpness in the scanned image when Digital ICE or a similar infrared channel dust removal function is used. Kodachrome also has a pronounced relief image that can affect the IR channel. The absorption of the cyan dye extends into the near IR region, and thus this layer is opaque to IR. Kodachrome interacts with this infrared channel in two ways. Many scanners use an additional infrared channel to detect defects, as the long wave infrared radiation passes through the film but not through dust particles. Typically, dust, scratches, and fingerprints on the slide are detected and removed by a scanner's software. However, a calibration with a particular Kodachrome target is necessary for accurate color reproduction.
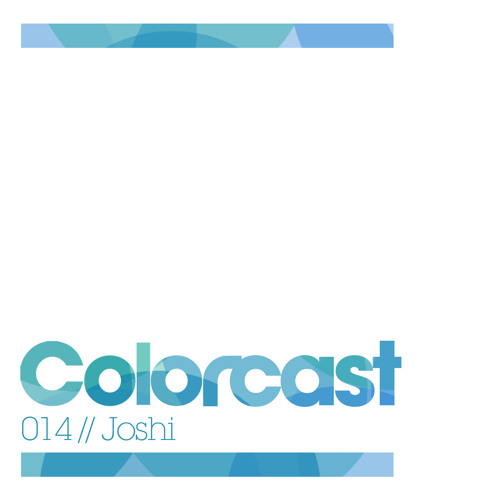
#Colorcast dyes software#
Some software producers deliver unique Kodachrome color profiles with their software to avoid this. Scanning Kodachrome transparencies can be problematic because the film tends to scan with a blue color cast.
#Colorcast dyes iso#
A 35mm Kodachrome transparency, like other 35mm transparencies on films of comparable ISO rating, contains an equivalent of approximately 20 megapixels of data in the 24 mm x 36 mm image.
